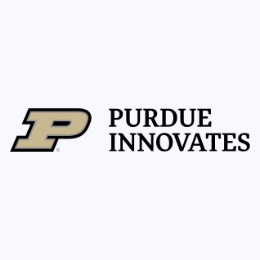
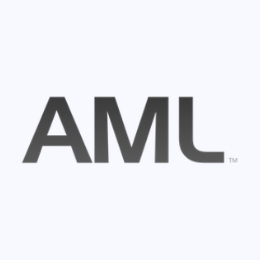
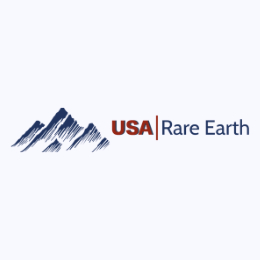
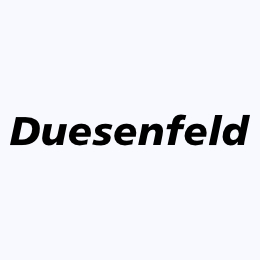
Our chromatographic purification and separation process is capable of producing two distinct critical mineral product lines: high purity rare earth element oxides and lithium-based battery cathode active materials (CAM).
ReElement recovers and refines 99.99%+ pure magnetic rare earth elements from all rare earth containing resources. This core refining technology is a highly sustainable and economically favorable process that leverages chromatography to separate and purify rare earth elements.
ReElement recovers and refines cathode active materials such as lithium, nickel, cobalt, and manganese from mineral ores, brines, recycled batteries, black mass, and battery manufacturing waste. The refining process is the same for both rare earth elements and critical battery elements relying on resin packed chromatography columns to separate and purify critical minerals.
ReElement’s novel use of chromatography for purification and separation of critical minerals is highly adaptable to the form and chemistry of the resources being refined. Our feedstock adaptability is enabled by our predictive model guided design which analyzes intrinsic parameters of various process inputs rapidly calculating the best possible design to refine any given material.
Our primary processing focus are the various rare earth and critical battery element containing mineral ores. We process and refine lithium-containing spodumene and lepidolite ores in addition to the rare earth ores such as monazite sands and basnasite ores. The low-cost and high-sustainability of our refining technology makes it far superior to current industry methods of processing critical mineral ores.
Production of highly pure lithium from from mineral brines coupled with the scalability and low operational costs make our refining technology ideal for modular deployment in remote regions with brine pools or co-located alongside desalination facilities for continuous refinement.
Current recycling regulations are unrestricted and often lead to a loss of critical materials in either landfilling or smelting. Our technology unlocks the large latent value contained within the magnets and lithium batteries of all end-of-life materials from the grams of critical materials in consumer electronics to the metric tons in an F35 or nuclear submarine.
ReElement currently processes kilograms of lithium-iron-phosphate (LFP) and nickel-manganese-cobalt (NMC) black mass unlocking and recovering the valuable lithium content trapped alongside metallic impurities. Our LFP recovery process purifies lithium back to battery-grade carbonate or hydroxide depending on the requirements of our partners.
Our refining platform can be scaled according to the needs of any specific mining or manufacturing site. This modularity is made possible by the use of highly efficient chromatography columns densely packed with metallic binding resin. To scale up or down, ReElement simply adds or removes processing columns.
ReElement’s critical mineral refining platform relies on chromatography and its inherently efficient mass transfer and large interfacial area for metallic separation to occur. This innovative technology coupled with our first-principles based design enables our process to rapidly adapt to input type and scale to required specifications without large upfront capital investment. With almost all inputs chemicals and water reused or recycled, our technology is the complete circular refining solution for both rare earth elements and critical battery minerals.
Our technology platform leverages a proven industrial purification method called chromatography. Commonly found in food processing and pharmaceutical manufacturing, ReElement has adapted the method to recover and refine high-purity rare earth and critical battery elements.
Our core technology uses chromatography columns densely packed with microporous binding resin. The large inter-spacial binding area for separation and purification to occur in and on the resin enables the process to have a small physical footprint shrinking the refining process down from what was multiple stadiums in size to a single 1 meter by 2 meter processing column.
High efficiency and low chemical consumption contribute to cost-effective production of ultra-high purity materials. Our rare earth and critical battery element production has exceeded 99.99% purities without any additional post-processing.
ReElement deploys the most sustainable mineral refining technology operational today with zero harsh chemicals, zero waste water produced, 25% less processing water, 75% less processing energy and 70% less total carbon emissions.